Service at Langzauner:
The competence you need for efficient plant operation
Langzauner provides an extensive range of services for smooth, efficient plant operation at our customers. Whether troubleshooting faults, ordering spare parts or scheduled maintenance – our service team is on hand to support you in every situation and provide sustainable solutions.
Service offerings at Langzauner
Langzauner’s worldwide service has been developed to meet the needs of our international customers. We combine short response times and problem-solving skills with offers for future-proof plant operation on volatile, international markets.
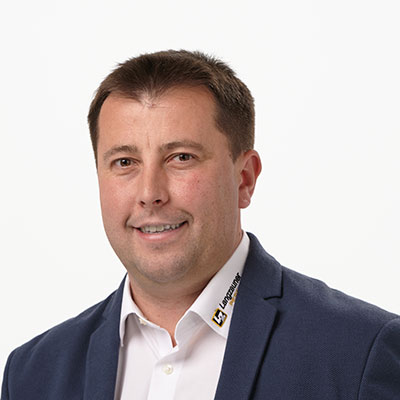
Reinhard Berger
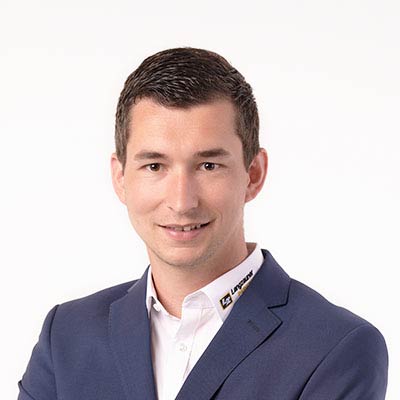